In the complex world of construction, accurate material takeoff is the bedrock of successful project management. It’s the painstaking process of quantifying every single component needed for a build, from the largest structural beams to the smallest screws. Traditionally, this has been a manual, often tedious, and error-prone exercise, leading to costly delays, budget overruns, and frustrating rework. Enter Building Information Modeling (BIM) – a transformative digital approach that is fundamentally changing how material takeoff is performed, ushering in an era of unprecedented accuracy, efficiency, and collaborative power.
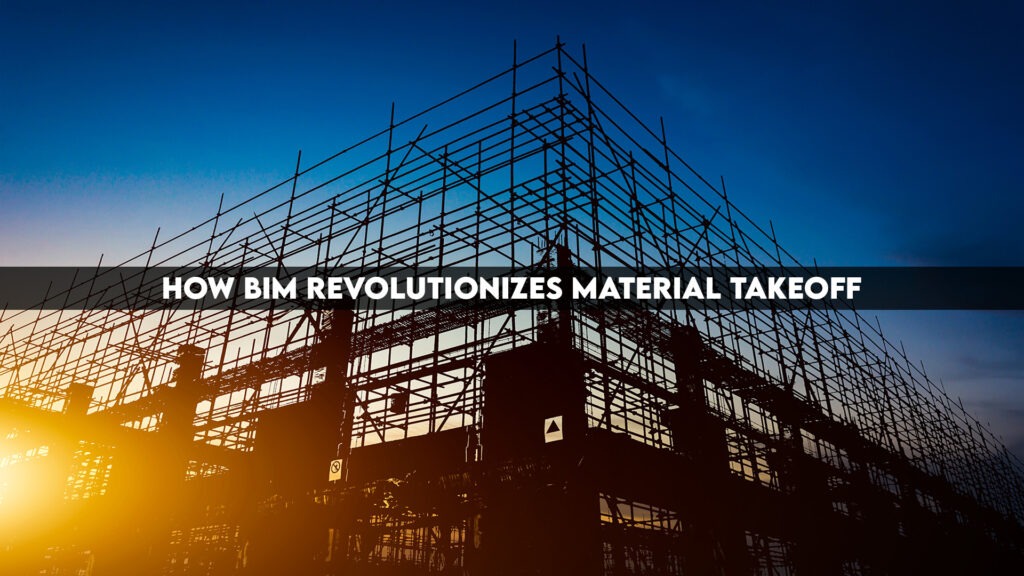
The Old Way: A Recipe for Headaches
Imagine a bustling construction site. Before BIM, a quantity surveyor or estimator would pour over stacks of 2D drawings – floor plans, elevations, sections, painstakingly measuring and counting every element. A wall, for instance, wouldn’t just be a wall; it would be a series of measurements for its length, height, and thickness, followed by calculations for the number of bricks, the volume of mortar, the area of plaster, and so on. Any design change, even a minor one, meant starting the process all over again.
This traditional method was inherently susceptible to human error. Misinterpretations of drawings, calculation mistakes, overlooking small details, or simply losing track amidst hundreds of pages could snowball into significant problems down the line. The disconnect between design changes and the takeoff process often led to outdated estimates, causing friction between designers, contractors, and suppliers. The quest for accurate material quantities was often a race against time, prone to stress and inefficiencies.
BIM: A Digital Twin for Seamless Quantification
Building Information Modeling fundamentally shifts this paradigm. Instead of separate 2D drawings, BIM creates a 3D digital model of the entire building, where every element – walls, doors, windows, pipes, even furniture – is represented as an intelligent object. These objects are not just visual representations; they carry a wealth of embedded information: dimensions, material types, specifications, fire ratings, and even cost data. This “information-rich” environment is what makes BIM a game-changer for material takeoff.
The power of BIM lies in its ability to automatically extract and generate material schedules and quantity reports directly from the model. When a wall object is placed in the BIM model, the software inherently understands its material composition, its volume, its surface area, and its associated components. This eliminates the need for manual measurements and tedious calculations.
Also Read: Building the Future, Naturally: The Rise of Hempcrete and Bio-Based Materials
How BIM Enhances Accuracy: Precision by Design
The core benefit of BIM in material takeoff is its profound impact on accuracy. This isn’t just about speed; it’s about getting it right, every single time.
- Single Source of Truth: With a BIM model, there is one central, shared data repository. All project stakeholders work from the same up-to-date model. Any change made by an architect, structural engineer, or MEP designer is immediately reflected across the entire model. This eliminates discrepancies that arise from working with outdated drawings or multiple versions, ensuring that the material takeoff is always based on the most current design. This concept of a “single source of truth” drastically reduces errors.
- Automated Data Extraction: BIM software automates the process of extracting quantities. Instead of manual counting, the software identifies and quantifies objects based on their properties. This virtually eliminates human calculation errors, a significant source of inaccuracies in traditional methods.
- Rich Information Tied to Objects: Every element in a BIM model has detailed attributes. A door, for example, isn’t just a rectangular opening; it’s a specific type of door, with its dimensions, material (wood, steel, glass), hardware specifications, and even its manufacturer. This granular level of detail ensures that the takeoff is precise, accounting for every minute component.
- Visual Verification: The 3D nature of BIM allows for visual verification of quantities. Estimators can “see” the elements they are quantifying, making it easier to spot omissions or double-counts that might go unnoticed in a flat 2D drawing. This visual clarity fosters better understanding and validation.
- Clash Detection for Material Optimization: BIM’s clash detection capabilities are invaluable. By identifying conflicts between different building systems (e.g., a pipe clashing with a structural beam) before construction begins, BIM helps avoid costly rework and material waste. This proactive problem-solving ensures that the materials ordered are truly what’s needed, minimizing excess or shortages.
Boosting Efficiency: Time is Money (and BIM Saves Both)
Beyond accuracy, BIM dramatically boosts the efficiency of the material takeoff process, leading to significant time and cost savings.
- Speed and Automation: What once took days or weeks of manual effort can now be generated in minutes or hours. The automated extraction of quantities frees up quantity surveyors and estimators to focus on higher-value tasks, such as value engineering, cost analysis, and supplier negotiations.
- Rapid Iterations and Revisions: Design changes are an inevitable part of construction. In a traditional workflow, each revision meant a complete re-do of the takeoff. With BIM, changes in the model automatically update the associated quantities. This rapid revision capability is a huge time-saver and allows for more agile project management.
- Enhanced Collaboration and Communication: BIM fosters a collaborative environment where all disciplines work on a common model. Architects, structural engineers, MEP engineers, and estimators can share information seamlessly. This improved communication reduces misinterpretations and speeds up decision-making, leading to a more efficient overall workflow.
- Better Cost Control and Budget Management: With precise and up-to-date material quantities, project managers can develop more accurate budgets from the outset. This robust cost control allows for better financial planning, reduces the likelihood of budget overruns, and enables more informed procurement decisions.
- Improved Procurement and Supply Chain Management: Accurate material takeoffs provide procurement teams with precise lists of required items. This leads to more efficient ordering, reduced waste from over-ordering, and fewer delays due to material shortages. Suppliers can also provide more accurate quotes based on reliable data.
- Reduced Rework and Waste: By identifying potential issues like material clashes or quantity discrepancies early in the design phase, BIM significantly reduces the need for costly rework on site. This, in turn, minimizes material waste, aligning with sustainable construction practices.
Implementing BIM for Material Takeoff: A Strategic Approach
Adopting BIM for material takeoff isn’t just about purchasing software; it’s a strategic shift that requires careful planning and implementation.
- Training and Skill Development: Investing in proper training for estimators, quantity surveyors, and project managers is crucial. Understanding how to navigate BIM software, extract data, and interpret BIM models is fundamental to success.
- Standardization and Libraries: Developing consistent BIM standards, including naming conventions and object libraries, ensures that data is uniform and easily extractable. A well-defined BIM execution plan is essential.
- Integration with Other Software: BIM’s true power is unlocked when it integrates seamlessly with other project management, estimating, and enterprise resource planning (ERP) software. This creates an end-to-end digital workflow.
- Pilot Projects: Starting with pilot projects can help organizations gradually adopt BIM for material takeoff, identify potential challenges, and refine their processes before a full-scale rollout.
- Cultural Shift: Embracing BIM requires a cultural shift towards greater collaboration and a digital-first mindset across all project teams. It moves away from siloed workflows to an integrated project delivery approach.
The Future is Now: BIM as the Standard
The role of BIM in streamlining material takeoff is no longer a futuristic concept; it is rapidly becoming the industry standard. As construction projects grow in complexity and the demand for efficiency and sustainability increases, BIM’s capabilities will become even more indispensable. From reducing estimation time by upwards of 50% to slashing material waste, the tangible benefits are clear.
BIM empowers construction professionals with unparalleled visibility and control over project costs and resources. It moves material takeoff from a reactive, error-prone task to a proactive, data-driven process, allowing teams to make smarter decisions, optimize procurement, and deliver projects on time and within budget. In essence, BIM isn’t just a tool; it’s the blueprint for a more efficient, accurate, and sustainable future for the entire construction industry.